rovides broad prospects for lightweight exterior walls
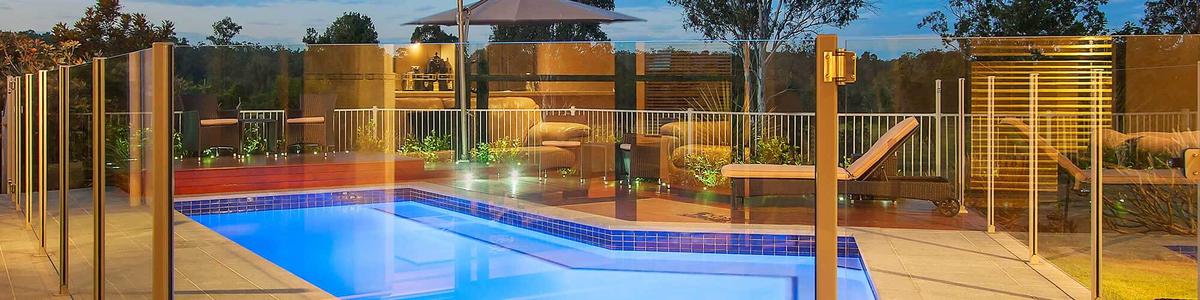
Thin heat strengthened glass provides broad prospects for lightweight exterior walls, reduces the use of raw materials, and at the same time opens up a new perspective for architectural expression with its excellent optical quality and high flexibility. Due to the structural problems mainly caused by the low rigidity of the product, the realization of projects with thin heat strengthened glass as a structural element has so far been limited.
This article attempts to circumvent this problem by using examples of past all-glass projects and current research projects to explore the possibility of structural application of thin glass as a membrane element. It is impractical to use thin glass as a compression member because the risk of buckling is greater than the threat of excessive stress.
As an alternative, it is recommended to use it as a tensile member, supported by examples from academic and industrial research projects. In this case, a new type of glass holder was introduced, which can transmit load without moment to the heat strengthened glass.
In contemporary architecture, opaque architectural elements are increasingly being replaced by transparent elements. The desire for architectural transparency has made the use of glass as a building material more and more popular. Most importantly, with the expected growth, the realization of heat strengthened glass structures is becoming more and more challenging, as evidenced by many existing all-glass projects around the world.
Today, the development of the aforementioned production technology allows us to produce heat strengthened glass with a thickness as low as 25 microns (Schott AG, 2019). In this case, thin glass opens up a whole new perspective for architectural glass design, but it also brings challenges that need to be overcome. Many projects have been implemented in the past and now, which can be used as a guide for implementing this relatively novel product.
Generally speaking, glass with a thickness of less than 2mm is thin glass. Although thin or ultra-thin glass is commonly used in other industries, such as the electronics industry, the standard glass thickness used in construction is usually 2 to 12 mm. This chapter describes the possibilities and challenges of thin glass implementation in the built environment.
Compared with ordinary glass, thin glass stands out because of its lower thickness at the same density, reduced raw material usage and light weight. These aspects not only provide potential economic advantages, but also contribute to the sustainability of the overall building due to the reduced use of raw materials. This applies not only to the glass itself, but also to the entire building, because the light weight of the glass also reduces the weight on the supporting structure.
Another aspect worth mentioning is that thin heat strengthened glass has higher flexibility and excellent optical quality compared to glass of traditional thickness. Rather than seeing flexibility as a disadvantage, it is better to see it as an opportunity to open the way for the design of more transparent and visually appealing structures. If glass is used to make complex shapes, they will be limited, either due to the potentially high cost of the hot bending process, or due to technical limitations, such as the minimum bending radius of cold formed glass that is too large (Topcu 2017).
In addition to academic research projects, a large number of industrial research projects involving cold bending of thin heat strengthened glass have been carried out, proving the extent to which thin glass can be deformed and the possibilities brought about by this characteristic.
A study conducted by Seele in 2012 studied the minimum achievable radius of thin glass cold-formed during the lamination process (Figure 01). The test was carried out with two chemically strengthened glass panels, each with a thickness of 1 mm and an SGP interlayer of 0.89 mm. First, the finite element model was used to model the sample to determine the smallest possible bending radius, and then it was successfully implemented in the bending test. The bending is performed using a 3D printed mold with a radius of 300 mm. The glass radius increases to a final value of 450 mm after relaxation, which is unthinkable for glass of conventional thickness (Kloker 2012).
A further study showing the bendability of thin glass is the flowing heat strengthened glass sculpture proposed and designed by Carpenter / Lowings Architecture & Design and Eckersley O'Callaghan Ltd (Figure 02). This example shows a frameless thin glass sculpture in which cold bending is done by spot fixing at the corners of chemically strengthened glass elements. Due to the cold bending process, compared with hot bending glass, the resulting optical distortion is small. Another effect obtained by the resulting shape is the stiffness of the geometry, which allows the glass to stand independently without the help of additional sub-structures.
Although thin glass is promising for the future, it has not been implemented in any project as a structural component so far. This can be attributed to multiple reasons. This article only focuses on the limiting factors from a structural point of view.
The first challenge to overcome is the low bending stiffness of the element and its high sensitivity to buckling, which is true in every thinner material. However, in the case of glass, its brittle behavior increases the risk of serious consequences in the event of a failure, which requires additional attention.
Among the above-mentioned challenges we face, lack of stiffness is undoubtedly the most in need of attention, because the structural concept is completely dependent on it. Generally, the application of glass in construction is limited to panels used as building envelopes and in some cases as barriers. Since the plate is subject to bending, thin glass lacks rigidity due to its low thickness and therefore does not offer much potential in this way. A possible and more effective way to fully utilize the potential of this product is to apply membrane theory.
Membrane theory describes the state of a structure in which the load is mainly transmitted in the form of normal force, and the bending moment is so small that it can be ignored. Over time, it has proven to be a very effective method of transferring loads with minimal material. The advantage of this effect over the plate is that the stress is evenly distributed throughout the cross section. Unlike the case of plates, stress peaks or uneven stress distribution in the cross-section are avoided, and structural materials can be fully utilized (Figures 3 and 4).
Common geometric shapes that allow membrane behavior are arches, shells, domes, and barrels, among other shapes. All these geometric shapes are based on the principle of catenary curve: the form that appears when the chain is loosely fixed at both ends. If it is assumed that the suspension chain is glued and turned upside down at the connection point of each link, the resulting geometry corresponds to the geometry of the thrust line (Figure 5).
The thrust line (LT) is an imaginary line through which the normal force flows in the structure. It includes two forces: the weight of the structure (W) and the horizontal thrust (HT). The resultant force of the two is thrust (T), acting in the direction of the thrust line (Figure 6).
In an ideal arch, the normal force passes through its axis, which means that this special shape will provide maximum stability under its own weight. In contrast, in a barrel or dome, the thrust line will slightly deviate from the center of the cross section. If the thrust line is far from the center, a pulling force will be generated. However, as long as the thrust line remains within the middle third of the cross section, the structure will remain stable (Dutton 2013).
The geometric shape of the thin shell can be recognized by a similar concept of the suspension model. This method is also described as structure search. Then replace the imaginary chain with cloth, which is fixed to each support. The shape formed by the weight of the cloth forms the basis of common shell structures, including monolithic domes, grid shells, or saddle roofs.
The shape of the arch is controlled by the thrust line and corresponds to the catenary line. For external loads that may be asymmetric (such as wind), the geometry needs to be further optimized. Unlike the arch shape, the shape of the thin shell does not need to adapt to the load. If the shape of the arch is adjusted according to the load, the arch can only transmit load without bending moment, and the shell has the ability to carry loads without bending moment, as long as it is supported in the plane of the shell and avoids concentrated loads (Schober 2015 ).
Seele has implemented all-glass projects in the past, where the heat strengthened glass acts as a compression or in-plane shear member. These projects emphasize that even using technology more than 20 years ago, it is possible to create cost-effective all-glass structures.
These forces are the result of the self-weight of the structure and the prestress caused by the cable network that spans between each node along the nodes. A key factor in the development of this structure is the material properties of glass, which can transmit compression forces greater than tensile forces. Although this method has proven to be effective, the risk of buckling caused by the slender structure limits the achievable possibilities of the glass dome (Ludwig & Weiler 2013).
The all-glass barrel vault roof of the Maximilian Museum was completed in 2002, forming a self-supporting structure on a 37m x 14m historical courtyard with a total of 527 glass panels (Figure 8). The only component that complements this all-glass enclosure is a tubular frame that defines the edge of the barrel vault. The single-curvature shell structure forming the barrel vault can economically prefabricate the same panes. Compressive stress is transferred to the structure at the nodes.
To this end, each pane is supported on the node plate by a stainless steel cap installed at the corner. A pin with an adjusting screw in the center of the node is used for positioning the plate to form a structural connection with the steel cap. Each pane is made of laminated safety glass, which consists of two layers of 12 mm heat strengthened glass, measuring 1.16 mx 0.95 m (seele GmbH 2020).
Both of the above projects show an example of glass as a compression member. However, since the shell structure requires a minimum thickness to prevent compression buckling, this concept is not ideal for thin glass applications. One possible solution to overcome this obstacle is to reverse the structure back to its original orientation under its own weight.
In this way, the glass will be subjected to tensile stress. As mentioned in the case study of Weltbild Dome, glass is more effective in compression than in tension, but due to the excess stress, the risk of bending to thin glass is greater than the risk of failure. Therefore, the load is transmitted more effectively in the form of tension, because the unstable effect of the compression force is avoided, thereby eliminating the risk of buckling.
A lot of research is being conducted to study the performance of glass when used as a tensile member. Their findings are critical to understanding how much thin glass structures can be added to the architectural branch.
This chapter introduces two exhibits that demonstrate the ability of heat strengthened glass to withstand tension.
Research conducted by TU Darmstadt shows an example of an existing flexible cable net structure concept inspired by Frei Otto's roof of the Munich Olympic Park. As the roof cover is replaced by thin glass, the structure allows for more transparency while maintaining light weight. Therefore, the cable net determines the shape of the structure according to the prestress level of each cable, and the glass acts as a conformal covering to form a transparent weatherproof roof structure and transfer loads (Figure 9).
Due to the large deformation of glass related to its thickness, the assumptions of linear plate theory are no longer applicable, and geometric nonlinear effects need to be considered for accurate calculations. The glass bears the combination of bending force and film force. In order to ensure a continuous structure with a smooth transition between each glass element, the elements are linearly supported by continuous clamping rods (Figure 10, Peters et al., 2019).
The concept of using thin heat strengthened glass as a structural membrane may have been most effectively demonstrated in the "Gravity" project of the glass technology site in 2018. The idea of starting with the membrane under tension means that an innovative way of transferring the required load is devised. Around that time, bonding systems such as Dow's TSSA began to propose different methods to get force in and out of the glass surface: when thicker glass systems were used previously, minimizing fixation meant developing point fixation and focusing the force on Point.
The exhibit includes two glass panels, laminated with two sheets of 2 mm thin glass and SGP, and bonded to a stainless steel edge strip, which is suspended from a tripod structure. This component brings the 1.5-ton swing car close to the podium. The glass panel is 1m x 2m and consists of two thermally strengthened laminated glass panels. The glass bonding details are one-sided, relying entirely on the adhesive connection to transfer the load.
The swing of automobile mass is simulated by Define Engineers using nonlinear transient dynamic finite element analysis. The suspension point on the top of the glass allows the car to rotate 360 degrees and swing 15 degrees from the vertical to any direction, all suspended on high-strength steel rods with a diameter of 9.5 mm. This is modeled in the analysis as a pendulum with an initial displacement equal to the maximum swing angle and a minimum damping of 5%.
The dynamically amplified tension in the system (Figure 11) is used to design all the components of the exhibition. The non-linear effect of the glass under tension (15kN) offsets the bending, otherwise the bending may occur due to the glass's own weight or any other later load, just like a rope in tension, it stays straight and can resist lateral loads. The result of using permanent tension in the glass is that perfectly straight glass panels increase the drama of the exhibition.
The hanger and all brackets are carefully designed to avoid bending the glass by external forces. This is achieved by using an offset steel bracket (Figure 12), which introduces a moment in the steel structure, but the line of reaction is aligned with the centerline of the glass. This results in an effective bending in the glass with zero tension.
In addition, the pivot on the top is specially designed to achieve maximum movement and minimum restriction to reduce the twisting force in the glass panel. All in all, in order to keep the film loaded only in the glass, all attention is focused on the details of the system to release as much heat strengthened glass as possible while keeping the system stable.
The heat-strengthened glass is glued to the stainless steel strip inside the hanger detail using Dow TSSA, and then connected to the car. The top is a specially designed and manufactured suspension detail. Laminated glass uses SGP as an intermediate layer, and the heat-strengthened glass has a fracture mode that allows the load to be transferred to the supporting glass plate through the intermediate layer. Please note that the details are one-sided to show the transparency of the fixed details and maintain the clarity of the glass front. This shows how to present it in the architectural environment of the actual project.
One of the main features of the project is the transparent connection between the glass and stainless steel bracket, which is made of the Dow Chemical Company DOWSIL™ Transparent Structural Silicone Adhesive (TSSA). The permanent stress in the TSSA layer is estimated to be approximately 0.6 N/mm², which is further increased to approximately 0.7 N/mm² due to the dynamic effect of the rocking car. The last exhibit in the Glass Technology Live section is shown in Figure 13.
Seele used 400mm x 600mm thin glass samples provided by Glaston to conduct structural performance tests to confirm the reliability of TSSA. The 300 mm x 40 mm test TSSA bonding area must transmit a permanent load of 4.5 kN, resulting in a local peak stress of approximately 0.6 N/mm².
For short-term experiments, increase the force until the glass or TSSA fails. The maximum tensile force of the first three samples reached an average value of 53.8 kN (Figure 14). The fourth sample (PK4) was deliberately subjected to additional bending, so it was not included in the average value.
After reaching the maximum force, the entire laminate failed. The entire TSSA surface was covered with heat strengthened glass shards, indicating that the adhesive layer was still intact after the maximum force was reached (Figure 15).
The long-term experiment was carried out for a week under the force required by the structure, and the same force was increased by 50%. The sample can withstand the load without any visible change. Subsequently, the glass layer was broken to test the remaining capacity of the laminate. Although a single crack propagated, complete failure did not occur.
Thin glass is a promising material. Through the application of traditional engineering design methods, combined with innovative materials that require innovative solutions, lighter, more transparent and more optically attractive structures can be created.
The purpose of this article is to demonstrate the advantages of this new product with its unique characteristics, such as light weight or high flexibility. In contrast, some challenges and constraints are mentioned, explaining the difficulties of implementing thin heat strengthened glass in the built environment, and the limitations set due to the inherent properties of the material.