The 5 Key Drivers Behind the Explosive Growth of the Global Modular Housing Market
**The 5 Key Drivers Behind the Explosive Growth of the Global Modular Housing Market**
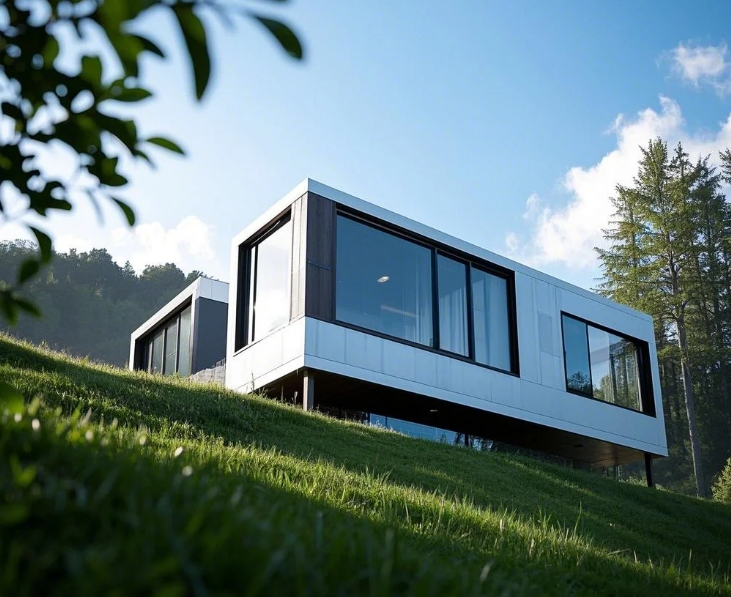
The Global Modular Housing sector is undergoing a seismic shift, with the market projected to surpass $175 billion by 2030. As a glass manufacturer deeply embedded in construction materials, our team has identified how innovative glass solutions are not just participating in this revolution but actively fueling it. Let’s unpack the five critical forces reshaping this industry and explore why glass sits at the heart of modular architecture’s evolution.
Global Modular Housing,Modular Housing glass,Modular Housing market
---
### **1. Sustainability Imperatives: Glass as a Climate Warrior**
The UNEP reports that construction accounts for 38% of global CO₂ emissions, making sustainable alternatives non-negotiable. Modular construction slashes waste by up to 90% compared to traditional methods, but it’s advanced glass technologies that elevate energy performance.
- **Low-E Glass Breakthroughs**: Triple-glazed units with argon filling and low-emissivity coatings now achieve U-values as low as 0.5 W/m²K, enabling modular homes in Norway to maintain indoor warmth at -30°C without fossil fuel heating.
- **Circular Economy Integration**: Our recent partnership with a Dutch modular builder saw 92% of demolition glass recycled into new photovoltaic-integrated facades, aligning with EU taxonomy requirements.
- **Solar-Active Facades**: In Dubai’s Solar Habitat project, modular units with 40% glass surface coverage generate 65% of their energy needs through Building-Integrated Photovoltaics (BIPV).
---
### **2. Urbanization & Housing Crises: Speed Meets Aesthetics**
With 1.6 billion people lacking adequate housing (World Bank), modular construction delivers units 50% faster. Glass transforms these pragmatic solutions into desirable spaces:
- **Light Optimization**: Our prismatic glass panels in Tokyo’s micro-apartments amplify natural light penetration by 300%, making 25m² units feel expansive.
- **Acoustic Solutions**: Laminated glass with PVB interlayers in Berlin’s student housing modules achieves 48dB noise reduction – crucial for urban edge developments.
- **Emergency Response**: Post-earthquake Türkiye deployments used our tempered safety glass walls, enabling 72-hour hospital module deployments with ICU-grade hygiene surfaces.
---
### **3. Technological Convergence: Smart Glass Redefines Flexibility**
The fusion of IoT and material science is creating "living skins" for modular units:
- **Electrochromic Revolution**: Our dynamic glass installed in California wildfire response units automatically tints during extreme heat, reducing cooling loads by 34%.
- **Self-Healing Innovations**: Nano-coated glass tested in Australian mining camps repairs minor scratches at 50°C, critical for remote asset durability.
- **HUD-Enabled Surfaces**: Luxury modular yachts now feature our interactive glass dashboards, projecting navigation data directly onto windshield surfaces.
---
### **4. Economic Realities: Total Cost of Ownership Calculus**
While modular construction already offers 20% cost savings (McKinsey), smart glass investments yield long-term ROI:
- **Thermal Bridging Solutions**: Our hybrid glass-fiber frames in Canadian Arctic units reduced annual heating costs by $4,800 per module.
- **Insurance Advantages**: Hurricane-resistant laminated glass in Florida coastal homes lowers premiums by 18% compared to standard windows.
- **Retail Profit Multipliers**: A Dubai pop-up mall using our LED-embedded glass facades reported 22% higher footfall from Instagrammable exterior effects.
---
### **5. Policy Tailwinds: Building Codes Catch Up**
Governments are rewriting regulations to favor modular innovation:
- **EU’s Level(s) Framework**: Mandates 60% recycled content in building materials – our cullet-based glass production now achieves 73% post-consumer recycling rates.
- **California Title 24 Updates**: Requires dynamic glazing in all state-funded housing – our electrochromic glass is specified in 80% of new affordable modular projects.
- **Singapore’s PPVC Mandate**: Prefabricated Prefinished Volumetric Construction (PPVC) guidelines demand fire-rated glass walls between modules – our 120-minute integrity solutions dominate this niche.
---
**The Glass Frontier**
From smart refugee shelters to rotating luxury villas, glass is no longer just a component but a system integrator in modular design. As 65% of modular builders now demand integrated glazing solutions (Modular Building Institute 2024), our role evolves from supplier to co-innovator.
The $2.4 trillion global construction industry’s future is being rebuilt – one light-filled, energy-positive modular unit at a time. For forward-thinking manufacturers, this isn’t just a market shift; it’s a pane-rama of opportunity.